While you think about a 3D-printed dwelling, you in all probability image a boxy concrete construction.
As 3D printing’s reputation has grown within the development trade — due to its effectivity in relation to time, vitality and price — carbon-intensive concrete has grow to be the go-to constructing materials.
However a mission in Maine has set its sights on one thing completely different: a neighborhood of 600-square-foot, 3D-printed, bio-based homes crafted from supplies like wooden fibers and bioresins.
The goal: a fancy of 100-percent recyclable buildings that can present houses to these experiencing houselessness.
In late 2022, an initiative between the College of Maine and native nonprofit Penquis unveiled its prototype — BioHome3D, the primary 100-percent recyclable home. Now, the pioneering mission is working towards finishing its first livable housing complicated.
It is going to be absolutely bio-based, which means all supplies might be derived from residing organisms resembling vegetation and different renewable agricultural, marine and forestry supplies.
Causes to Be Cheerful takes a better have a look at the science and innovation behind the 3D printer creating these progressive buildings.
Bio-based supplies are designed to provide houses at scale
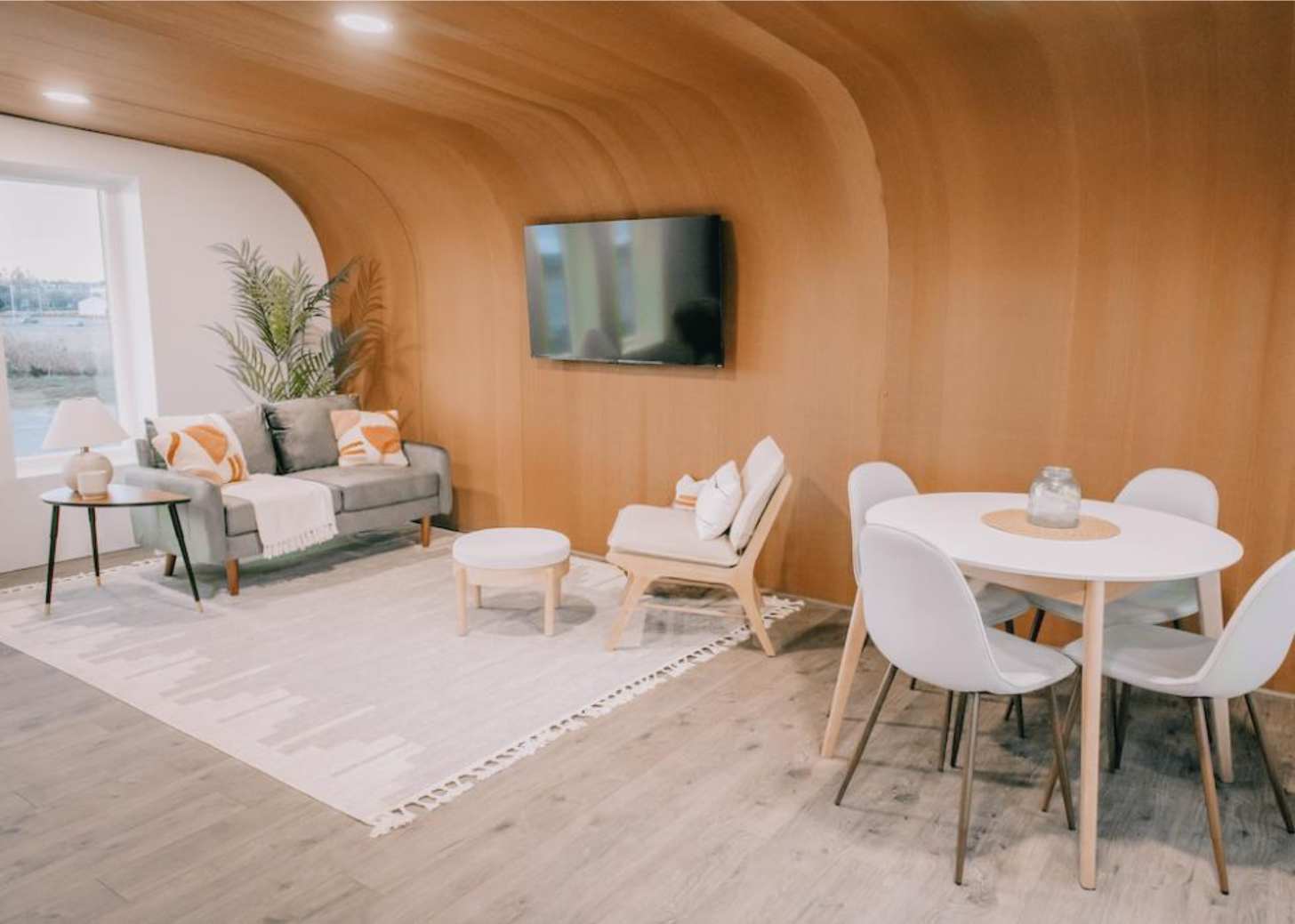
Because the supplies are all 100-percent recyclable, so grow to be the buildings.
The supplies are additionally all renewable.
And because of its pure composition, the house acts as a carbon sink, sequestering 46 tons of carbon dioxide per 600-square-foot unit.
The supplies for this mission will primarily come from wooden left over by native mills. “The wooden fiber materials that is used within the combine is basically waste wooden right here in Maine,” says Jason Fowl, director of housing improvement for Penquis.
Fowl is referring to what’s referred to as wooden residuals: supplies that, he explains, “pulp mills or different sawmills both landfill, discard or set off to the aspect and decay.”
In line with the College of Maine, the state’s sawmills produce almost a million tons of wooden residuals yearly.
Since every 600-square-foot unit requires roughly 10 tons of wooden residuals, 100,000 housing models may theoretically be produced yearly utilizing simply sawmill residuals.
The College of Maine’s Superior Constructions and Composites Heart acquired $3.3 million in funding for this mission final yr, and its collaboration with Penquis has got down to construct a ready-to-live neighborhood with 9 3D-printed houses for individuals experiencing houselessness.
Because the crew undergoes the ultimate regulatory hurdles, Fowl anticipates that homes might be able to reside in as early as this spring.
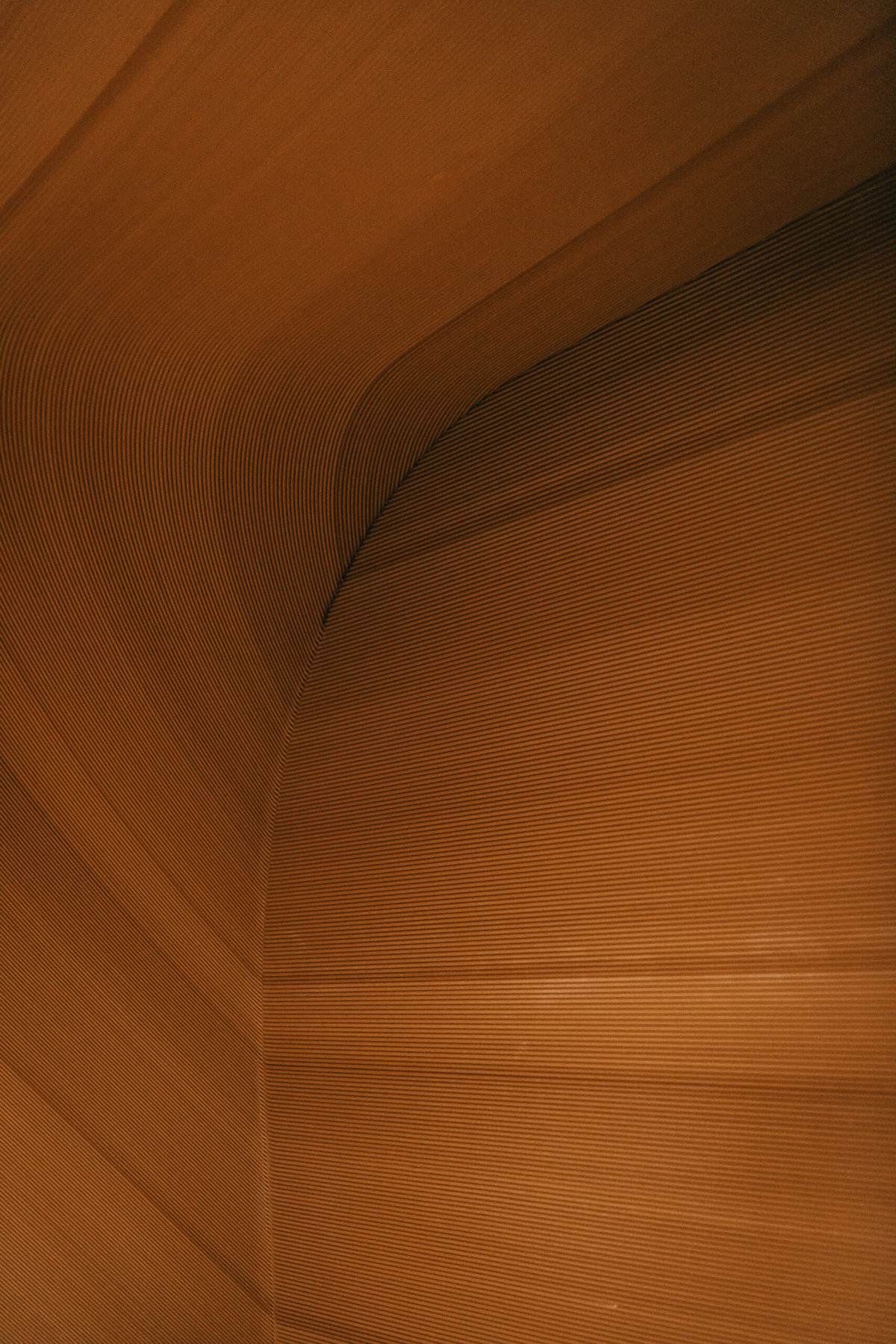
As soon as this pilot mission is accomplished and the crew on the College of Maine reaches full industrial capability, Fowl says the crew will be capable of print a house in as little as two days.
“That would come with the shell of the home — the roof, partitions, flooring system,” Fowl explains. “Lengthy-term [infrastructure projects] may embrace cupboards, counter tops, bathtub fixtures. And what will get me so enthusiastic about this mission is that the expertise is not simply fixing a neighborhood drawback, it might be replicated around the globe.”
Dr. Habib Dagher, govt director of the Superior Constructions and Composites Heart, confirms that the expertise is meant to be extensively replicated.
“The aim of this analysis is to create a system for establishing houses that alleviates strains on the availability chain and addresses labor shortages, whereas offering economical and sustainable housing,” says Dr. Dagher.
“This expertise can be utilized wherever on this planet that has entry to bio-based uncooked supplies. We’re targeted on scaling up manufacturing expertise to drive down prices and enhance availability.”
And after enduring a yr of maximum climate in Maine, with sensors reporting temperatures starting from 1 diploma to 105 levels Fahrenheit, BioHome3D met all sustainability, power, and sturdiness necessities for US constructing codes, in addition to the design necessities of the Worldwide Code Council code.
“Doing this mission in a spot like Maine, which has a number of the most excessive temperatures within the continental US, is important as a result of it may show that this materials can endure large temperature swings,” says Sarah Goehrke, founding father of Additive Integrity, a consulting service that focuses on the examination and sustainable acceleration of commercial 3D printing.
“The truth that BioHome3D survived for a yr is essential proof going ahead.”
A solution to a worldwide housing disaster?
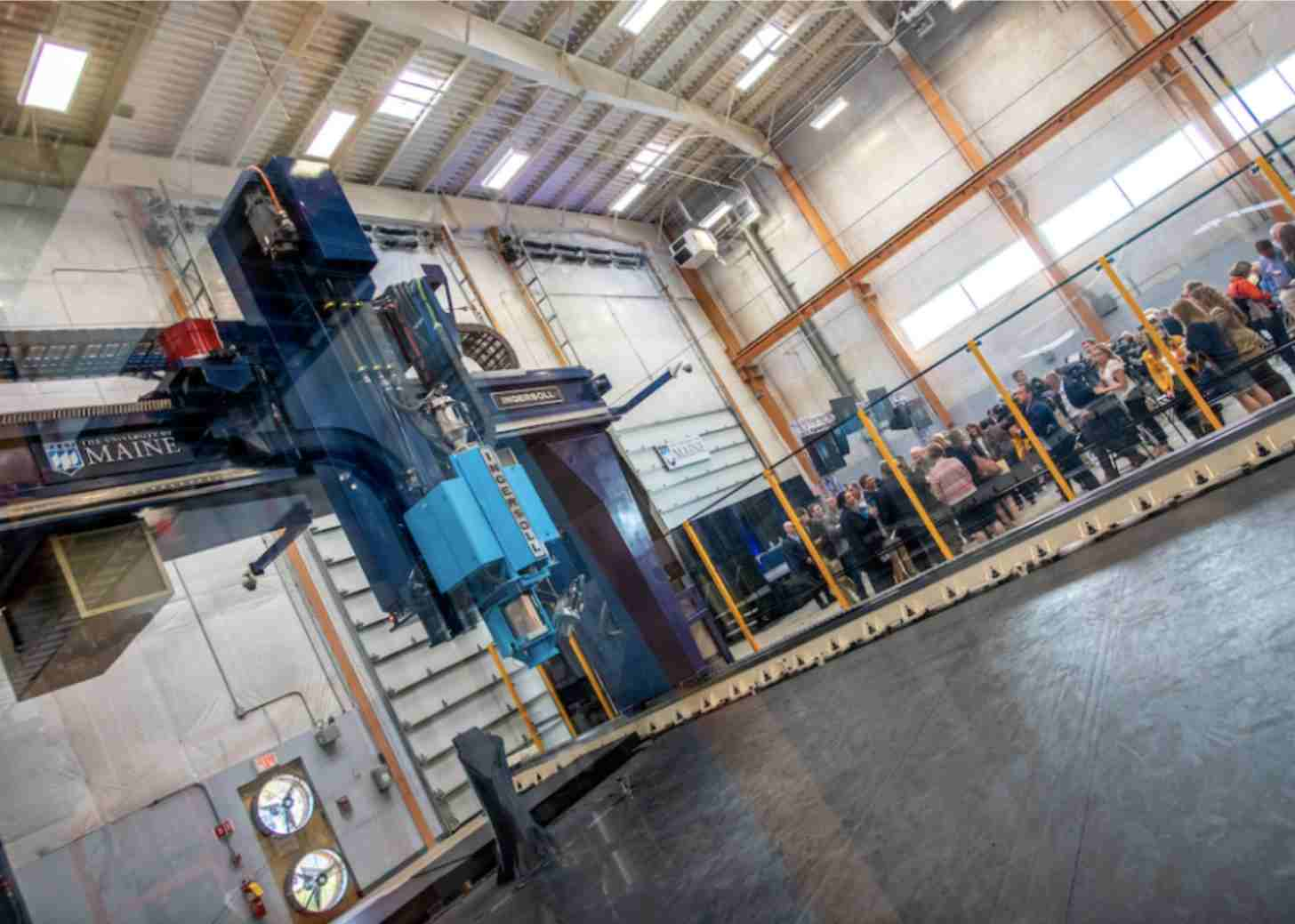
Preliminary printing speeds of 20 kilos per hour have since ramped as much as almost 500 kilos per hour, considerably lowering development prices.
This effectivity, mixed with native supplies, makes the method extra sustainable and resilient to international provide chain disruptions.
The mission is a well timed response to an already urgent and worsening international housing disaster. UN-Habitat predicts that by 2030, three billion individuals would require improved housing.
And with conventional development contributing a staggering 27 p.c of worldwide greenhouse emissions, less-polluting options might want to rise to the event.
In Maine, the necessity is obvious: the state is already experiencing a scarcity of 20,000 inexpensive housing models.
“What’s extra progressive about this mission [than other 3D housing initiatives] is each that it is bio-based, and that it is geared absolutely towards addressing the housing disaster,” says Goerhke.
3D-printed homes produce considerably much less waste than standard development, as builders are capable of print precisely the quantity of fabric they want for a given mission, and minimal house is required for storage supplies.
And with the power to retailer all supplies in the identical house, the vitality in any other case required to move supplies between websites is eradicated.
One forecast initiatives that the worldwide 3D development market will soar by 91 p.c from 2021 to 2028.
“Constructing many smaller buildings in a brief period of time is what the housing disaster wants to handle unhoused individuals and assist to create bigger communities fairly rapidly,” says Goerhke.
Header picture by the College of Maine Superior Constructions and Composites Heart
This text was initially printed by Stacker and was republished with permission.